Ford Fusion: Engine - 1.5L EcoBoost (118kW/160PS) – I4 / Engine. Disassembly
Special Tool(s) /
General Equipment
 |
100-001
(T50T-100-A)
Slide Hammer |
 |
300-OTC1819E 2,200# Floor Crane, Fold Away |
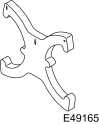 |
303-1097 Locking Tool, Variable Camshaft Timing Oil Control Unit TKIT-2010B-FLM TKIT-2010B-ROW |
 |
303-1502 Lifting Device Engine TKIT-2012A-FL TKIT-2012A-ROW |
 |
303-409
(T92C-6700-CH)
Remover, Crankshaft Seal TKIT-1992-FH/FMH/FLMH TKIT-1993-LMH/MH |
 |
303-748 Locking Tool, Crankshaft TKIT-2010B-FLM TKIT-2010B-ROW |
 |
307-005
(T59L-100-B)
Slide Hammer |
 |
308-375 Remover, Input Shaft Seal TKIT-2005U-M TKIT-1999-F/FLM/LT |
 |
310-206 Remover, Fuel Injector TKIT-2009A-FLM |
Hot Air Gun |
Hose Clamp Remover/Installer |
Materials
Name |
Specification |
Motorcraft® Metal Brake Parts Cleaner PM-4-A, PM-4-B |
-
|
NOTICE:
Do not loosen or remove the crankshaft pulley bolt without first
installing the special tools. The crankshaft pulley and the crankshaft
timing sprocket are not keyed to the crankshaft. Before any repair
requiring loosening or removal of the crankshaft pulley bolt, the
crankshaft and camshafts must be locked in place by the special service
tools, otherwise severe engine damage can occur.
NOTICE:
During engine repair procedures, cleanliness is extremely
important. Any foreign material, including any material created while
cleaning gasket surfaces that enters the oil passages, coolant passages
or the oil pan, can cause engine failure.
NOTE:
Refer to exploded views in Description and Operation.
-
Remove the bolts and the flexplate. Discard the bolts.
-
Mount the engine to the engine stand.
-
Remove Special Service Tool: 300-OTC1819E
2,200# Floor Crane, Fold Away.
-
Remove Special Service Tool: 303-1502
Lifting Device Engine.
-
Remove the coolant hose.
Use the General Equipment: Hose Clamp Remover/Installer
-
Remove the coolant hose.
Use the General Equipment: Hose Clamp Remover/Installer
-
Detach the wiring harness retainer and disconnect the electrical connector.
-
Disconnect all the coolant hoses.
Use the General Equipment: Hose Clamp Remover/Installer
-
Remove the coolant hoses.
Use the General Equipment: Hose Clamp Remover/Installer
-
Disconnect the PCV hose couplings and remove the hoses.
Use the General Equipment: Hose Clamp Remover/Installer
-
Remove the bolts and the A/C compressor.
-
Remove the bolts and the bracket.
-
-
Remove the nut, stud, stud bolt and the generator.
-
Remove the bolt and the accessory drive belt idler pulley.
-
-
Detach the retainers and disconnect the CKP sensor electrical connector.
-
Remove the stud bolt and position the wiring harness aside.
-
-
Detach the wiring harness retainer and remove the retainer.
-
Disconnect the electrical connectors and position the wiring harness aside.
-
Detach the wiring harness retainers and disconnect the electrical connectors.
-
Detach the wiring harness retainers and disconnect the electrical connectors.
-
Detach the wiring harness retainers and disconnect the electrical connectors.
-
Position the cover and disconnect the CHT sensor wiring harness electrical connector.
-
-
Detach the retainers, disconnect the electrical connectors and remove the wiring harness.
-
Remove the oil level indicator.
-
Disconnect the vacuum hose and retainer.
-
-
Remove the nut and the coolant outlet. Discard the nut.
-
Detach the retainers and position the vacuum hose aside.
-
Remove the nuts, bolt and the brackets.
-
Inspect the coolant outlet O-ring seal.
-
-
Remove the stud bolts and the vacuum pump. Discard the stud bolts.
-
Remove the bolts and the engine lifting bracket.
-
Remove the bolt and stud.
-
Remove and discard the vacuum pump gasket.
-
-
Detach the retainers and remove the TC wastegate control hose.
-
Remove the nut, bolt and the bracket.
-
Remove the retainers and position the TC coolant tube aside.
-
Remove the retainers and the TC coolant tube.
-
-
Remove and discard the TC coolant tube O-ring seals.
Material: Motorcraft® Metal Brake Parts Cleaner
/ PM-4-A, PM-4-B
-
Remove the bolts, stud bolt and the CAC.
-
NOTE:
Bolts remain captured in the intake manifold.
Remove the bolts and the intake manifold.
-
NOTE:
Note the position of the component before removal.
Remove the bolts and the VCT oil control solenoids.
-
NOTE:
The O-ring seals are to be reused unless damaged.
Inspect the VCT oil control solenoid O-ring seal.
-
-
Remove the bolts and the ignition coil-on-plugs.
-
Remove the bolts and the CMP sensors.
-
NOTE:
Replace any damaged coil-on-plug assemblies.
Inspect the coil-on-plug.
-
Loosen the flare nuts and remove and discard the high-pressure fuel tube.
-
Remove the retainers and the high-pressure fuel pump. Discard the retainers.
-
Remove and discard the high-pressure fuel pump O-ring seal.
-
Remove the high-pressure fuel pump tappet.
-
Inspect the high-pressure fuel pump tappet.
-
Disconnect the electrical connectors and remove the wiring harness.
-
NOTICE:
Pull out the fuel rails in the direction of the fuel injector axis or damage may occur to the fuel injectors.
NOTE:
Use compressed air and remove any dirt or foreign
material from the cylinder head, block and general surrounding area of
the fuel rail and injectors.
NOTE:
When removing the fuel rails, the fuel injectors may
remain in the fuel rails but normally remain in the cylinder heads and
require the use of a Fuel Injector Remover tool to extract.
Remove the bolts and the fuel rail assembly.
-
NOTE:
Take extra care when handling the components.
NOTE:
Remove any of the fuel injectors that remained in the fuel rail.
Remove clip and any of the fuel injectors that remained in the fuel rail.
-
Remove and discard the fuel injector clip.
-
NOTE:
Remove the fuel injectors that remained in the head.
Using the special tools, remove the fuel injector.
Use Special Service Tool: 307-005
(T59L-100-B)
Slide Hammer.
, 310-206
Remover, Fuel Injector.
-
NOTICE:
Do not set the valve cover sealing surface face down on a
bench as the check valve and splitter leg is susceptible to breakage.
Remove the bolts as shown in sequence and remove the valve cover.
-
Remove and discard valve cover gasket.
-
NOTICE:
Use a heat gun to soften the flange sealant, this will
aid in the removal of the fuel pump mounting bracket. Failure to follow
these directions may result in damage to the fuel pump mounting bracket.
-
Remove the bolts in sequence shown, heat and break the
adhesive bond and remove the high-pressure fuel pump drive unit.
Use the General Equipment: Hot Air Gun
-
Remove and discard the O-ring seal.
-
NOTICE:
Use a heat gun to soften the flange sealant, this will
aid in the removal of the fuel pump mounting bracket. Failure to follow
these directions may result in damage to the fuel pump mounting bracket.
-
Remove the engine cover mounting stud.
-
Remove the bolts and the stud.
-
Heat and break the adhesive bond and remove the brake vacuum pump cap.
Use the General Equipment: Hot Air Gun
-
Remove the retainer and the oil cooler. Discard the retainer.
-
NOTE:
Note the position for installation.
Detach the retainer, remove the bolts and the KS.
-
-
Remove the bolt, disconnect the coupling and remove the crankcase vent oil separator inlet pipe.
-
Remove the bolts and the crankcase vent oil separator.
-
Remove and discard the oil pressure switch.
-
Remove the nut, stud and the thermostat housing.
-
Inspect the thermostat housing O-ring seal.
-
Remove the bolts and the TC heat shield.
-
-
Remove the TC oil return tube to TC bolts.
-
Remove the TC oil return tube to engine block bolt and remove and discard the TC oil return tube.
-
Remove and discard the TC oil return tube gasket. Clean the sealing surface.
-
Remove the nuts, retainer and the TC. Discard the nuts.
-
Remove the and discard the TC oil supply tube assembly, including the bolt, the sealing washers and the O-rings seals.
-
Remove and discard the TC mounting gasket and studs.
-
NOTE:
Note the position for installation.
If equipped with block heater, remove the nut and the block heater.
-
Remove the stud bolt and position the cover from engine front cover aside.
-
-
Remove the bolts and the coolant pump pulley.
-
Remove the engine mount stud.
-
Remove the engine front cover bolts.
-
Remove the engine front cover.
-
NOTE:
Note the different lengths of the bolts.
Remove the bolts and the engine mount bracket.
-
NOTE:
Only rotate the crankshaft in a clockwise direction.
Rotate the crankshaft pulley until the timing marks at the 11 o'clock position.
-
Remove the engine plug bolt.
-
NOTE:
The Crankshaft TDC Timing Pin will contact the crankshaft and prevent it from turning past TDC. However, the crankshaft can still be rotated in the counterclockwise direction. The crankshaft must remain at the TDC position during the crankshaft pulley removal and installation.
Install Special Service Tool: 303-748
Locking Tool, Crankshaft.
-
NOTE:
Only rotate the crankshaft clockwise direction.
Rotate the crankshaft slowly clockwise until the crankshaft balance weight is up against the TDC Timing Peg. The engine is now at TDC.
-
Remove the bolt and the crankshaft pulley. Discard the bolt.
-
Remove the retainer and the CKP sensor.
-
NOTE:
The timing mark of each VCT unit must be at the 12 o'clock position.
Install Special Service Tool: 303-1097
Locking Tool, Variable Camshaft Timing Oil Control Unit.
-
WARNING:
The timing belt tensioner spring is under load. Extra
care must be taken at all times when handling the tensioner. Failure to
follow this instruction may result in personal injury.
-
Rotate the timing belt tensioner clockwise.
-
Install a holding pin.
-
Remove the timing belt.
-
Remove the crankshaft sprocket.
-
Using the special tools, remove and discard the crankshaft front seal.
Use Special Service Tool: 308-375
Remover, Input Shaft Seal.
, 100-001
(T50T-100-A)
Slide Hammer.
-
WARNING:
The timing belt tensioner spring is under load. Extra
care must be taken at all times when handling the tensioner. Failure to
follow this instruction may result in personal injury.
Remove the retainer and the timing belt tensioner
-
Remove the bolts and the coolant pump. Discard the bolts.
-
Remove and discard the coolant pump gasket.
-
Remove Special Service Tool: 303-1097
Locking Tool, Variable Camshaft Timing Oil Control Unit.
-
NOTE:
Use an open-ended wrench to hold the camshafts by the hexagon to prevent the camshafts from turning.
Remove the VCT unit caps.
-
NOTE:
Use an open-ended wrench to hold the camshafts by the hexagon to prevent the camshafts from turning.
Remove the bolts and the VCT units. Discard the bolts.
-
Using special tool, remove and discard the camshaft seals.
Use Special Service Tool: 303-409
(T92C-6700-CH)
Remover, Crankshaft Seal.
-
NOTICE:
Use a heat gun to soften the flange sealant, this will
aid in the removal of the camshaft mega cap. Failure to follow these
directions may result in damage to the camshaft mega cap.
NOTICE:
Do not pry on camshafts when removing or damage to the camshafts may occur.
NOTE:
Note the location and orientation of each camshaft
bearing cap and the position of the camshaft lobes on the No. 1 cylinder
for installation reference.
NOTE:
Retain the original camshaft bearing cap bolts for reuse
when measuring the valve clearance, if needed, during assembly.
-
Remove the bolts and the camshaft caps.
-
Heat and remove the mega cap.
Use the General Equipment: Hot Air Gun
-
Discard the camshaft caps bolts.
-
Remove the crankcase vent oil drain tube.
-
Inspect crankcase vent oil drain tube and replace if damaged.
-
Remove and discard the O-ring seal.
-
NOTE:
If the camshafts and valve tappets are to be reused,
mark the location of the valve tappets to make sure they are assembled
in their original positions.
NOTE:
The number on the valve tappets only reflects the digits
that follow the decimal. For example, a tappet with the number 0.650
has the thickness of 3.650 mm.
Remove the valve tappets.
-
Inspect and install new components as necessary.
-
NOTE:
Make sure that the cylinder head is at ambient air temperature before removing the cylinder head bolts.
Remove the bolts in the sequence shown and the cylinder head. Discard the bolts.
-
Remove and discard the cylinder head gasket.
-
Remove and discard the dowels.
-
Check the cylinder block and cylinder head distortion.
Refer to: Cylinder Head Distortion (303-00 Engine System - General Information, General Procedures).
Refer to: Cylinder Block Distortion (303-00 Engine System - General Information, General Procedures).
-
Remove Special Service Tool: 303-748
Locking Tool, Crankshaft.
-
Remove the oil pan bolts.
-
Using the pry pads, remove the oil pan.
-
Remove the bolts and the crankshaft rear seal.
-
Remove the bolts and the oil pump screen and pickup tube.
-
NOTE:
The O-ring seal is to be reused unless damaged.
Inspect the oil pump screen and pickup tube O-ring seal.
-
Remove the bolts and the oil pan baffle.
-
NOTE:
Note the position of the 3 different lengths of the bolts for installation.
-
Remove the two M6 x 55 mm bolts.
-
Remove the three M6 x 35 mm bolts.
-
Remove the three M6 x 25 mm bolts and remove the oil pump.
-
Remove and discard the oil pump gasket.
-
-
Clean the bolt holes for the oil pump with Motorcraft® Metal Brake Parts Cleaner to remove all residual oil.
Material: Motorcraft® Metal Brake Parts Cleaner
/ PM-4-A, PM-4-B
-
Use compressed air to remove any brake clean or oil in the oil pump bolt holes.
-
-
Before removing the pistons, inspect the top of the cylinder bores.
-
If necessary, remove the ridge or carbon deposits from each cylinder using an abrasive pad.
-
NOTE:
The connecting rod cap bolts are a torque-to-yield
design. The original connecting rod cap bolts will be used when
measuring the connecting rod large end bore during assembly. The
connecting rod cap bolts will be discarded after measurement.
NOTE:
Clearly mark the connecting rods, connecting rod caps
and connecting rod bearings in numerical order for correct orientation
for reassembly.
Remove the bolts and the connecting rod caps.
-
NOTE:
Do not scratch the cylinder walls or crankshaft journals with the connecting rod.
Using a connecting rod installer, repeat until all the piston/rod assemblies are removed from the engine block.
-
NOTE:
Mark the position of the parts, so they can be installed in their original positions.
Remove the connecting rod main bearings.
-
Inspect the pistons.
Refer to: Piston Inspection (303-00 Engine System - General Information, General Procedures).
-
NOTE:
The main bearing beam has 2 arrows pointing towards the front of engine for correct orientation for reassembly.
Remove the bolts in sequence shown and the main bearing beam.
-
NOTE:
If the main bearings are being reused, mark them in order for correct orientation and reassembly.
Remove the crankshaft main beam bearings.
-
Remove the crankshaft.
-
NOTE:
If the main bearings are being reused, mark them in order for correct orientation and reassembly.
NOTE:
The center bulkhead has the thrust bearing.
Remove the crankshaft main bearings.
-
Remove the bolts and the engine piston oil cooler valves.
Special Tool(s) /
General Equipment
303-1249Valve Spring CompressorTKIT-2006UF-FLMTKIT-2006UF-ROW
303-300
(T87C-6565-A)
Set, Valve Spring CompressorTKIT-1988-FESTIVAT88C-1000-STTKIT-1988-TRACERTKIT-2009TC-F
303-350
(T89P-6565-A)
Compressor, Valve SpringTKIT-1990-LMHTKIT-1989-FTKIT-1989-FMTKIT-1989-FLM
303-472
(T94P-6565-AH)
Adapter, Valve Spring CompressorTKIT-199..
Other information:
Special Tool(s) /
General Equipment
Tie Rod End Remover
Removal
NOTICE:
Suspension fasteners are critical parts that affect the
performance of vital components and systems. Failure of these fasteners
may result in major service expense. Use the same or equivalent parts if
replacement is necessary. Do not use a replacement part of lesser
quality or substitute design. Tighten fa..
Tuning a Station
You can use the tune or seek controls on
the radio bezel to select a station.
To tune a station using the
touchscreen, select:
A pop up appears, allowing you to type in
the frequency of a station. You can only
enter a valid station for the source you are
currently listening to.
You can press the backspace button to
delete the previously entered number.
Once you have entered..